
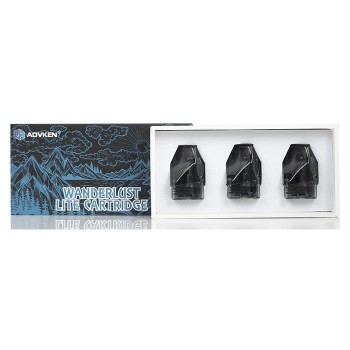
The last decade witnessed significant progress in the bioprinting arsenal with many ground-breaking innovations that makes 3D bioprinting one of the most exciting and promising technologies that could impact many medical applications. For example, the 3d bioprinter could be evolved as an integrated surgical tool for in situ printing ( 5). Therefore, the engineering of the modular 3d bioprinter is advancing with high-speed pace. 3d bioprinting benefits from the well-established printing technology.3d bioprinting is amenable to automation and scalable technology that would enable the mass production of tissue/organ from standard building blocks ( 4).3d bioprinting allows a high level of control and precise positioning of several cell types, thanks to the precise control position of the dispenser nozzle in the X–Y–Z space ( 1, 4), hence enabling accurate recapitulation of tissue/organ microstructure with high architectural complexity.However, bioprinting has a great potential to surpass the traditional tissue engineering techniques and can offer solutions to many existed technological hurdles such as: The progress in bioprinting technology is going separately through these techniques, and the real challenge is to integrate these technologies in an industrial scalable technology ( 1). 3D printing shares the three basic components with the conventional Gutenberg paper printing: the 3D model file to be printed (blueprint) is analogous to the text file, the bioink (which comprises cells and other bioactive materials) is analogous to the ink, and the 3d printer is analogous to the printer that deposit the ink on a substrate or print platform ( Figure 1). However, current tissue-engineering strategies lack the capability of fabrication of fully functional tissues and recapitulate their heterocellular structure ( 2, 3). Various techniques were utilized and developed, aiming to mimic the living tissue structure and function, such as scaffold fabrication, tissue culture, bioreactors, ECM self-assembly among others. In vitro, cells cannot arrange themselves in 3D structures like that in real tissue in vivo. 3D bioprinting benefited from several technologies such as tissue engineering, synthetic biology, micro/nanofabrication, and bioprocessing biomaterial production ( 1).

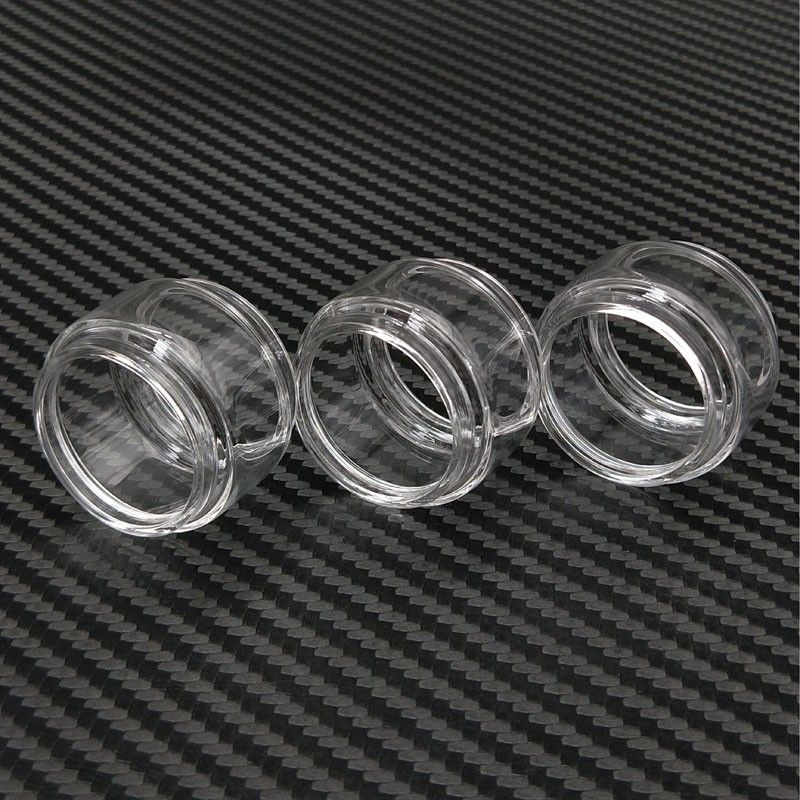
More recently, 3D bioprinting technology has emerged from the existing 3D printing, by utilizing life cells and gels as printing materials (bioinks) to create ex vivo and in vitro tissue models, which heralds' new frontiers in medicine.ģD bioprinting is the process of integrating living cells with biomaterials that allows controlled layer-by-layer deposition of cells/bioink, which is characterized by hierarchical structural properties, with maintained cellular viability in 3D space to create complex, multifaceted tissues. The successful implementation of AM in the healthcare industry has resulted in the development of surgical equipment, prosthetics, medical devices, and implants. This technology has recently infiltrated into many industries such as aviation, automobile, dental, electronics, and fashion. 3D printing is mostly well-known for custom-fabricating of industrial prototypes and parts using standard fabrication materials such as plastics and metals. Additive manufacturing (AM), the process of joining materials to make objects from computer-aided design (CAD) model data, such as 3D printing, shows a high potential to radically disrupt the global consumer market and trigger a manufacturing revolution in a broad spectrum of applications in many industry sectors.
